Unlocking Efficiency and Innovation: The Power of Modularization in Industrial Facilities
January 31, 2024
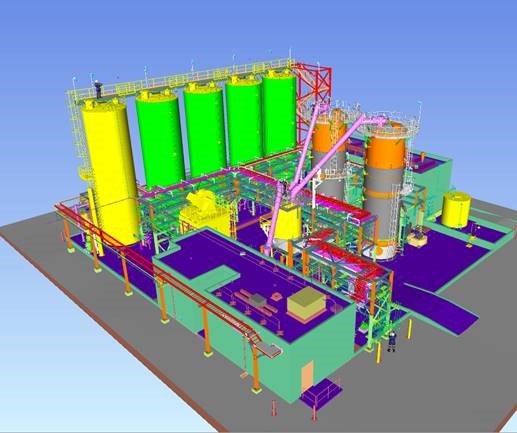
Modularization is a key solution for enhanced efficiency, cost savings, and streamlined operations. Modularization refers to the practice of designing and constructing a facility in a modular fashion, where components or units are pre-assembled off-site and then transported to the final location for integration, offering an abundance of benefits that redefine the way we build and operate industrial spaces.
Here, we unveil the essential steps for achieving effective modularization in facilities, providing a roadmap for industries aiming to stay ahead in today's competitive landscape.
The Modular Advantage: Why Modularization Matters
1. Cost Efficiency and Timely Operations:
· Reduced Construction Costs: Building modules in a controlled environment off-site can lead to cost savings due to economies of scale, efficient assembly processes, and minimized on-site construction time.
· Faster Project Completion: Modularization can significantly shorten project timelines, allowing facilities to become operational sooner. This can result in cost savings by reducing financing and labor costs.
2. Quality Control:
· Consistent Quality: Assembly in a controlled environment enables strict quality control measures, reducing the likelihood of errors or defects. Quality standards can be maintained more consistently across all modules.
· Standardization: Standardized designs and components contribute to enhanced reliability and easier maintenance, reducing the likelihood of defects and errors.
3. Safety:
· Reduced On-Site Risks: Safety is a top priority in any project. Since a significant portion of the construction work is done off-site, exposure to on-site hazards and risks is minimized. This can lead to a safer working environment for construction personnel.
4. Flexibility and Scalability:
· Adaptability: Modular designs are inherently flexible and can be easily adapted to changes in requirements or future expansions. Additional modules can be integrated to scale up production or modify the facility's functionality.
· Easy Relocation: Modular facilities can be disassembled and relocated if needed, offering flexibility in responding to changing market conditions or business needs.
5. Time Savings:
· Faster Construction: Construction and assembly of modules can occur concurrently with on-site preparation, reducing overall project timelines.
· Minimized Downtime: Rapid assembly and integration of modules not only accelerate project timelines but also minimize downtime during facility upgrades or expansions. This efficiency is a game-changer for industries where operational continuity is crucial for success.
6. Sustainability and Environmental Impact:
· Reduced Waste: Off-site construction often leads to reduced material waste by optimizing assembly processes and utilizing standardized components. Excess materials can be recycled or reused, aligning with sustainable practices and reducing the environmental footprint of industrial projects.
· Energy Efficiency: Modular facilities can be designed with energy-efficient features, contributing to overall sustainability goals. From improved insulation to the integration of renewable energy sources, modularization allows industries to embrace eco-friendly practices without compromising operational efficiency.
7. Improved Project Management:
· Streamlined Logistics: Planning and coordination of module transportation are more manageable compared to the complexities of coordinating various on-site construction activities. This streamlined approach enhances project management, ensuring deadlines are met with precision.
8. Risk Mitigation:
· Reduced Weather Dependency: Construction in a controlled environment minimizes the impact of adverse weather conditions, reducing weather-related delays and risks.
· Early Detection of Issues: Quality control measures can identify and address issues early in the construction process, minimizing the likelihood of costly rework. Industries can navigate uncertainties with greater confidence, safeguarding their investments and ensuring project success.
Embracing the Future: Steps for Effective Modularization in Industrial Facilities
Step 1: Comprehensive Project Assessment
Prior to commencing the modularization process, a thorough assessment of the client's needs, project requirements, and overarching goals are essential. Understanding the existing infrastructure, operational intricacies, and specific requirements of the facility is crucial to identify areas where modularization can provide the most significant impact. By conducting a thorough site analysis, companies can identify opportunities for modularization that align with their objectives. This initial step lays the foundation for a tailored and effective modularization strategy.
Step 2: Collaborative Design and Planning
Engaging in collaborative design sessions with stakeholders and fabricators is paramount to conceptualize modular solutions that not only meet the immediate needs of the facility but also allow for future scalability if being considered as part of a larger client delivery strategy, e.g. multiple similar plants. This stage focuses on breaking down the facility into modular components and establishing the design principles that will guide the entire process.
Step 3: Detailed Engineering Solutions
Customization is key when it comes to tailoring engineering solutions to meet the unique demands of each facility. Engineering teams leverage advanced technologies to develop detailed and customized designs that ensure structural integrity, safety, and operational efficiency. This step involves intricate planning to address specific challenges posed by the facility's layout, size, and function.
Step 4: Off-Site Module Fabrication
Once designs are perfected and prototypes validated, the focus shifts to off-site fabrication. Operating in controlled environments, manufacturers optimize assembly processes, adhere to strict quality control measures, and realize cost savings. Off-site fabrication accelerates project timelines, making it a pivotal step in the modularization process.
Step 6: Strategic Logistics Planning and Transportation
Efficient logistics planning is crucial for the success of modularization projects. Meticulous coordination for the transportation of modules from the fabrication facility to the construction site ensures timely delivery and minimizes transportation costs. Strategic planning in this phase minimizes transportation costs and ensures the timely delivery of modules for on-site integration.
Step 7: On-Site Integration and Commissioning
The on-site integration of modular components marks the culmination of the modularization process. Skilled engineering teams work collaboratively to ensure smooth assembly, adherence to safety protocols, and rigorous quality checks during the commissioning phase. This step marks the transition from conceptualized designs to fully operational modular industrial facilities.
Step 8: Continuous Monitoring and Support
The commitment to excellence extends beyond the integration phase. Continuous monitoring and support ensure the long-term performance, adaptability, and scalability of the modularized facility. Regular assessments and ongoing collaboration with clients further enhance the efficiency and functionality of the facility over time.
Embracing modularization holds the key to unleashing enhanced innovation, efficiency, and fostering a sustainable development process. By following these strategic steps, we can navigate the complexities of modularization, unlocking a future where facilities are not just constructed but optimized for success.
Συνδυάστε την καινοτομία και δημιουργήστε νέες δυνατότητες με το TWD.